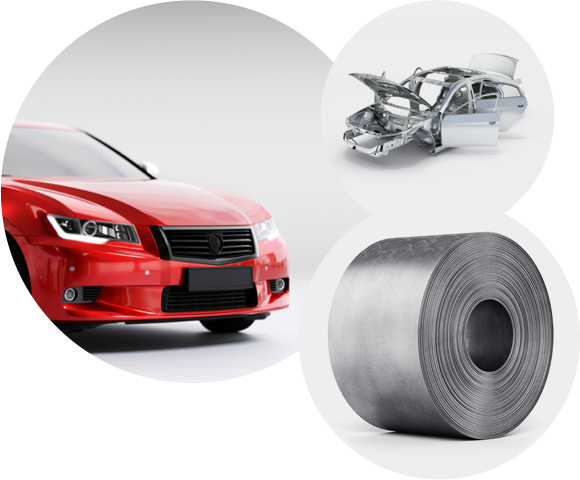
Benefits for the Automotive Industry
PRETEX® and POSTEX®
Actual and future demands of the automotive industry on the sheet metal surface structure
- Improved appearance of painted metal sheet surfaces
- Cost saving with paint systems without filler
- Improved formability
- Very low abrasion in the forming tool
- Stable surface characteristics along the entire strip width and length
*POSTEX registered trademark of Posco, PRETEX registered trademark of Salzgitter
Roughness | Waviness | |
Implemented in: Prüfvorschriften (PV) und Qualitätsrichtlinien | Raw material (flat sheet) acc. TL 218 | Deformed Sheet (Marciniak-cup with εp = 5% or part) acc. PV 1054 (draft) |
Measuring direction | transverse to R.D. | longitudinal to R.D. |
Exposed horizontal parts Process 2010 (no filter) | Ra = 0,9 – 1,4 μm RPc ≥ 75 1/cm | Wa0,8 ≥ 0,50 μm Upon Special agreement |
Exposed vertical parts Process 2010 (no filter) | Ra = 1,1 – 1,6 μm RPc ≥ 60 1/cm | |
Exposed parts with paint process including filter (5a with or without solvent) |
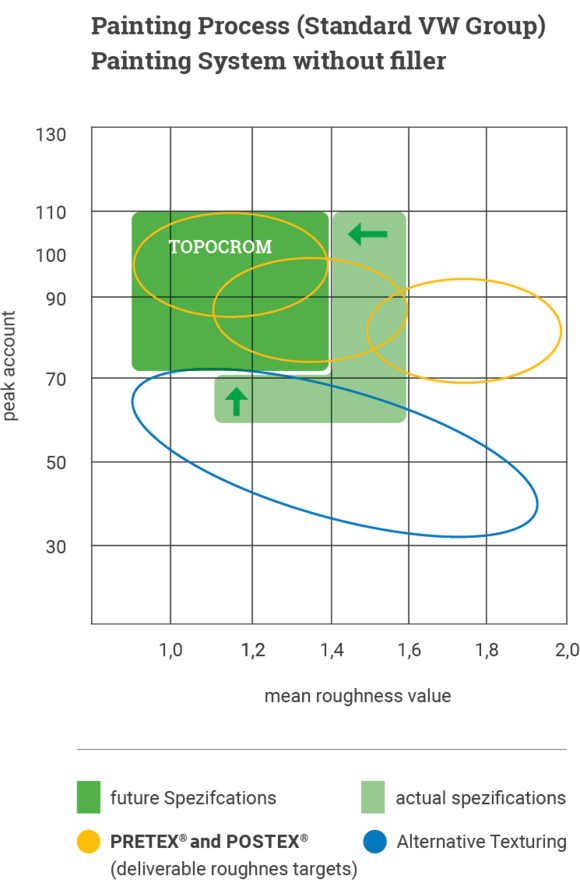
Data and Figures
Highly efficient painting processes
Due to the uniformity as well as the excellent waviness values a painting process without filler is possible for the metal sheet structured with Topocrom. This leads to thinner paint layers and cost savings.
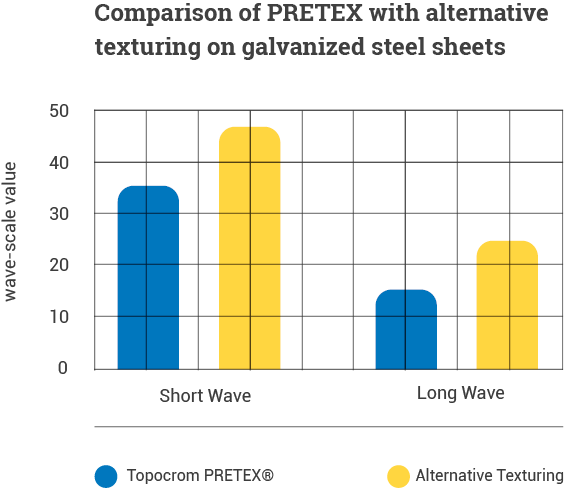
Appearance of the painted sheet
Short and long waves
Requirements for paint appearance
- Avoiding of Moiré-effects
- Avoiding of orange peel
Advantages of PRETEX® and POSTEX®
- Fine surface structure with high peak counts and low roughness
- Absolutely stochastic distribution
- Low wave-scan values
*POSTEX registered trademark of Posco, PRETEX registered trademark of Salzgitter
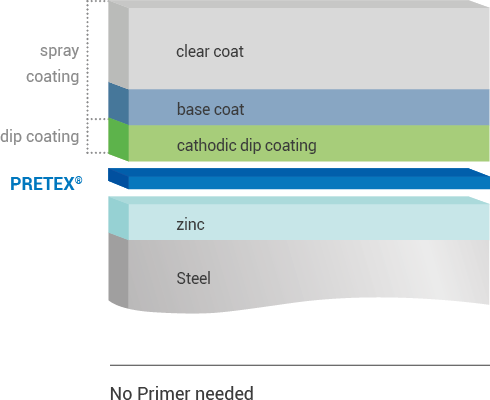
Challenge for Painting Process:
Saving the Primer
- Reduction of production costs, energy demand an CO2-emission
- Reduction of painting and drying steps
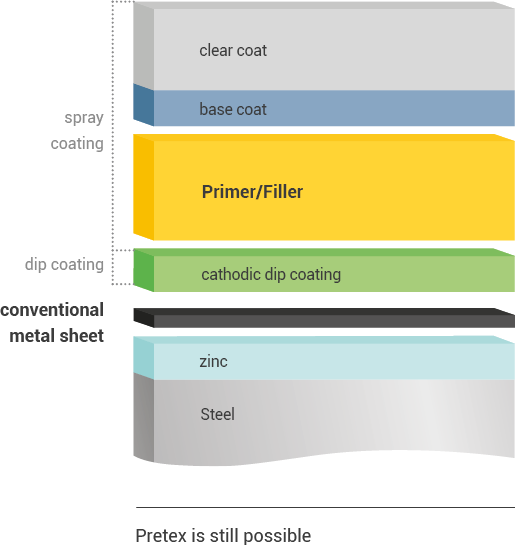
Important factor for surface structure of sheet metal Low waviness
- Filler and base coat are levelling the substrate, but are superposing the cathodic dip coat with a new waviness profile
- Cathodic dip coat is filtering the roughness characteristic, but waviness will be transferred. The capability for levelling the waviness will be reduced by saving the filler
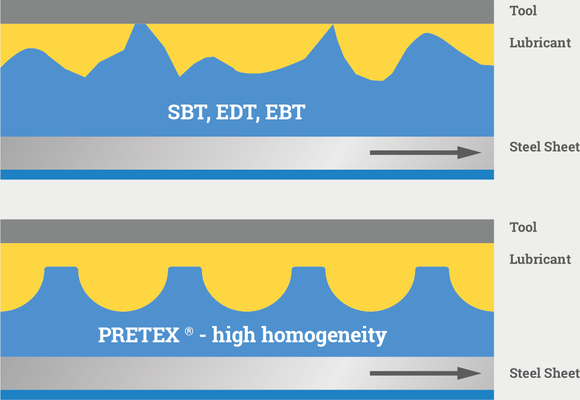
Excellent forming properties
Friction between steel sheet and tool
The surface morphology holds the lubricant and supports a hydrostatic and hydrodynamic lubrication towards reducing friction. A higher mean roughness value and lubrication pockets isolated from each other, serving as lubrication reservoirs, improve the friction and lubrication situation considerably.
An uniform distribution of the lubrication pockets and an uniform lubrication transport in the contact area between the tool and the sheet is just as decisive. Tests of various surface structures have proven that Pretex® texturized steel sheets reduce friction and transfer highest blank holder forces without appearance of cold fusing between tool and sheet surface. The deep drawing working area suitable for producing finished parts without wrinkles and fractures is thus extended.
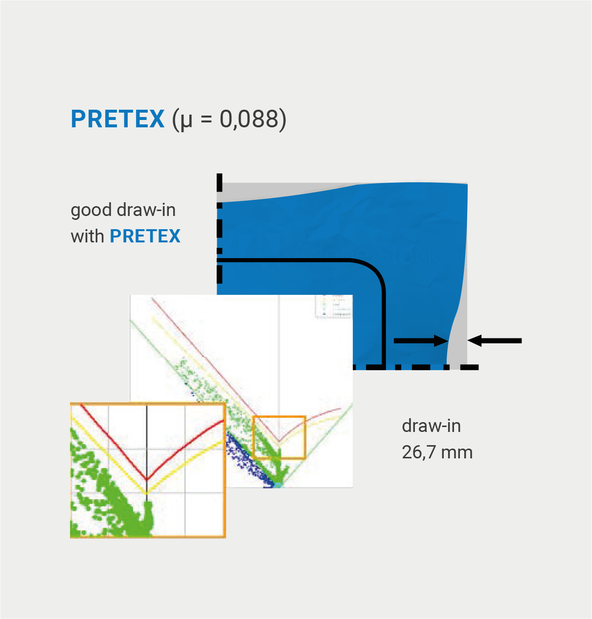
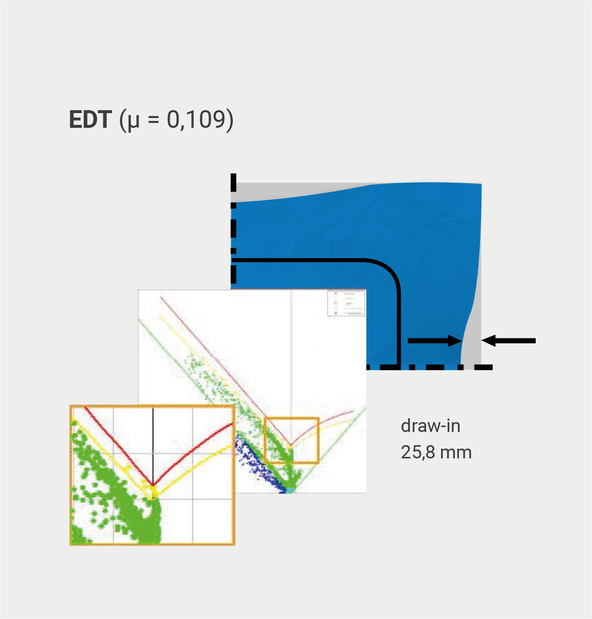